Principal
- FMA
- The Fabricator
- FABTECH
- Canadian Metalworking
Starting a metal additive manufacturing shop
Lessons learned and best practices include patience, resources, flexibility
- By Ryan Hayford
- Updated February 29, 2024
- March 4, 2024
- Article
- Metalworking
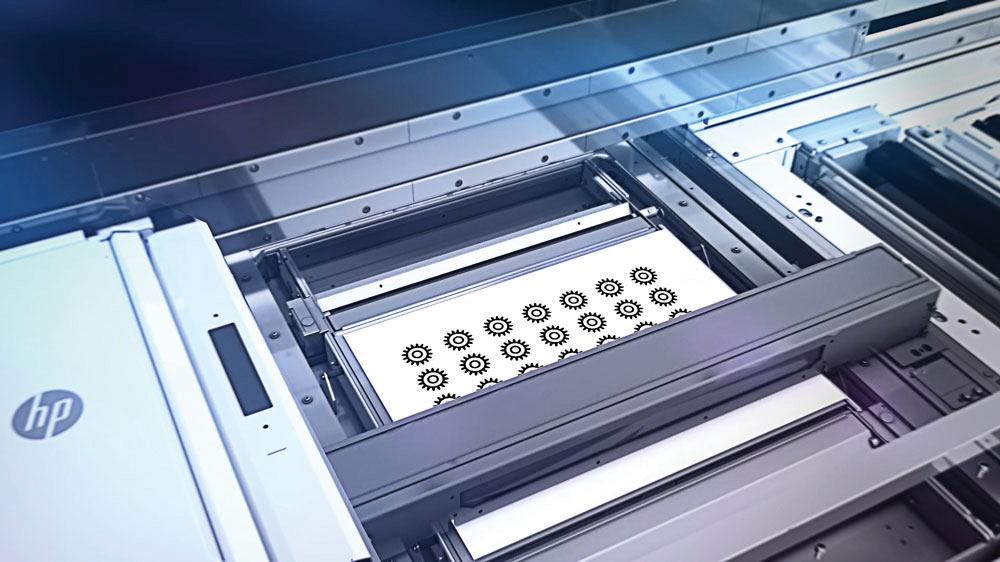
Metal binder jetting, as shown on this HP machine, is just one of many types of additive manufacturing processes. HP
What is the future of metal additive manufacturing (AM)?
Ultimately, the goal is to complement traditional casting and foundry operations with a cleaner and more flexible manufacturing method. This is a method that enables the design and production of high-performance parts with advanced materials faster and more cost-effectively than ever before.
Several AM technologies exist in the market today, most notably powder bed fusion (PBF), metal binder jetting, directed energy deposition (DED), and material extrusion. Each technology is compatible with a variety of material options and forms, such as powders, wires, and filaments.
As academia and the broader industry embrace additive technologies, significant resources have been allocated to developing this portfolio of materials. While this technology will never replace traditional manufacturing technologies, the design freedom afforded by AM will allow designers to create lighter and higher-performing products and more affordably manufacture lower-volume, complex parts.
There are several high-profile manufacturers in the automotive, aerospace, and heavy equipment industries that are committed to AM for several reasons. First, it’s an innovative platform that’s been consistently used by product developers and an excellent tool for prototyping. Second, the agility of the technology has proven to be a smart alternative for quick, on-demand parts that alleviate pressure in the supply chain for spares, repairs, and maintenance parts. Finally, the AM process is inherently less wasteful compared to alternative manufacturing methods, thus it supports the environmental stewardship goals of many businesses.
In fact, because of these reasons, many major original equipment manufacturers (OEMs) have aggressive initiatives to transition a certain percentage of their stock-keeping units (SKUs) to be produced additively.
However, adopting new technology, such as metal AM, comes with challenges that cannot be underestimated. For starters, the facility modifications and material handling requirements for operating and safely storing metal powders are strict (rightfully so) and expensive. Additionally, justifying a massive expense into metal AM requires a strong business case and it’s still a relatively unknown process amongst most manufacturers. Finally, the standardization of metal AM processes and materials is currently in development and not quite approved for critical applications. It requires a leap of faith, and in today’s economy, it’s better to be safe than sorry.
Many manufacturing newcomers that are considering opening an AM shop believe that many traditional manufacturers may not have the patience, resources, or flexibility to invest in capital equipment themselves. So they are offering this service instead by becoming and AM-only shop.
Understanding the Metal AM Landscape
To start an AM shop, it’s important to understand the different metal AM platforms and material options. For example, PBF is a versatile technology well suited for complex parts made from advanced materials. While suitable for one-off parts, there are throughput limitations with PBF. Alternatively, binder jetting may have fewer material sets, but it is much more scalable because of its speed and cost benefits. Each technology comes with specific design guidelines, facility, and safety requirements, so it’s important to identify strategic applications that align with the business objectives (reducing weight, improving performance, reducing carbon footprint). See Figure 1 for additional details.
Starting a metal AM shop from the ground up requires proper due diligence, patience, funding, and a strong foundation for the current and future business case.
For example, the average automobile is 50 per cent plastic, 31 per cent steel, and 9 per cent aluminum, so if you want to target the automotive spare parts industry with metal AM, then it’s imperative to have a technology capable of producing stainless steel and aluminum parts. In addition, those parts must perform as good, if not better, than the traditionally machined or cast metal parts. When determining the right technology, be sure to understand the density nuances, workflows, and facility considerations. Ask yourself the following questions to determine which technology is right for you:
- What is the primary (as well as secondary and tertiary) industry you anticipate generating the most business?
- What types of certification and material requirements are needed to operate within targeted industries?
- Will you offer design services, prototype development, production orders, or all the above?
- What skill sets (e.g., metallurgy, design for additive manufacturing) do you or your business have that can be applied?
- Is your facility capable of safely operating with metal powders?
Machine Installation
Once the decision is made to install metal AM machines, you must prepare to find or build a safe operating environment that will yield the highest productivity possible. This includes the construction of a temperature-controlled room for equipment operation and material storage. It also may include the installation of sintering furnaces as well as piping and electrical system to accommodate the hydrogen and nitrogen gas supply, if necessary.
Risk Assessment
One of the primary reasons why many major manufacturers continue to outsource their metal AM production needs is because of the significant explosion risks associated with metal powders.
Dust hazards and gas storage must constantly be checked and within specifications for proper use. Check with the American Society of Mechanical Engineers (ASME) and local municipality guidelines to develop the proper countermeasures to keep the facility safe and operational.
Facility Layout
Temperature-controlled rooms are important. Humidity and temperature swings can, for example, alter binder viscosity and powder-spreading behaviour, so it’s important to have an effective monitoring process. Good facility control systems analyze lowest explosive level percentage (LEL%), which is the lowest concentration of a gas or vapour that will burn in air; O2 levels; water cooling; and logs temperature and humidity records. It’s a necessary precaution, and the collected data is helpful in the root cause analysis process.
Quality Control
An AM shop, especially one for larger commercial use and critical applications, needs a robust quality control (QC) operation. This includes parameter development tools such as 3D scanning/CMM, mechanical testing, metrology, and other advanced QC technologies located in-house and offered as a service on behalf of customers.
Future Marketplace
Now more than ever, manufacturers are outsourcing to trusted partners and local suppliers who can competently and quickly get their production jobs done without major capital expenditure (CapEx) or overhead costs. This further illustrates the importance of relationships built on trust and reliability. After all, it’s important to be a partner, not just a provider.
The metal AM landscape is complicated and constantly evolving with new entrants into the market. There are so many processes, materials, risks, and hidden costs that begin to add up and overwhelm. Furthermore, the fear of obsolescence (planned or not) is enough to cause hesitation and make anyone reconsider.
This is why it is so important to lean on your resources and speak with the experts to conduct proper due diligence during the technology discovery stage. Whether you are a major OEM looking to bolster your advanced manufacturing capabilities or a start-up entrepreneur who wants to begin your own AM shop, it’s probably a safe bet to begin that journey with a contract manufacturer that has the experience and technical know-how to help navigate the process.
Bill Gates once famously stated, “The first rule of any technology used in a business is that automation applied to an efficient operation will magnify efficiency. The second is that automation applied to an inefficient operation will magnify the inefficiency.”
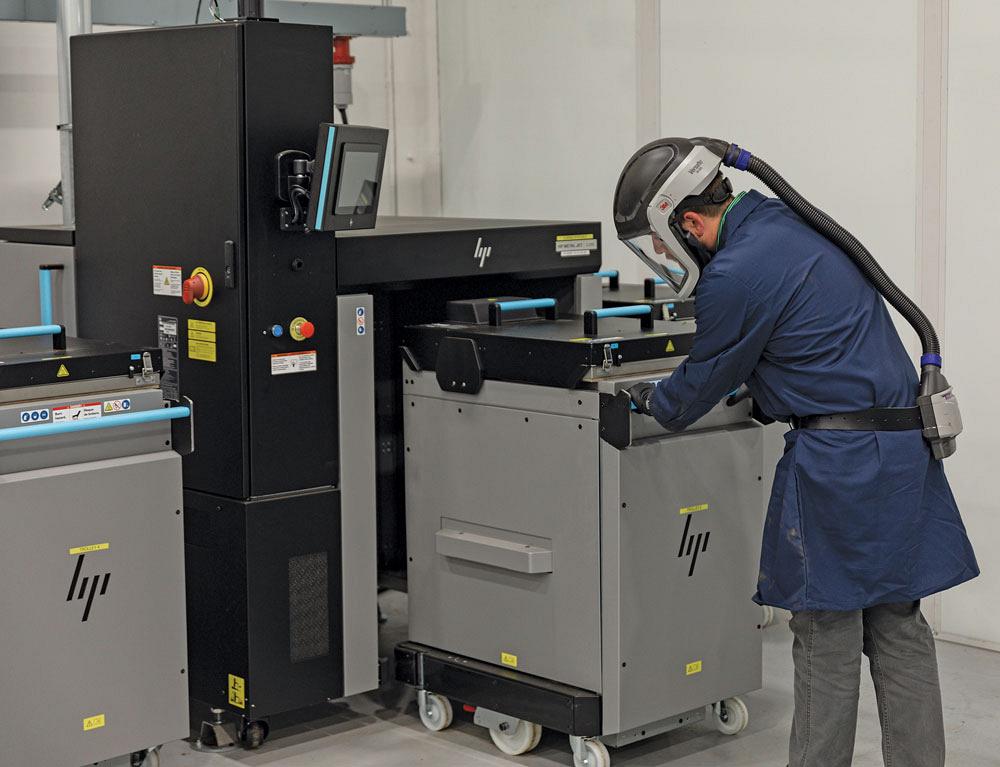
Material handling requirements for operating and safely storing metal powders are strict and expensive. HP and Endeavor 3D
If we apply the same formula, then we can acknowledge that we must operate effectively before we become efficient.
Contributing writer Ryan Hayford is a marketing and business development professional in the AM industry and principal at Hayford Consulting, www.hayfordconsulting.com.
About the Author
subscribe now
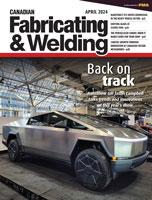
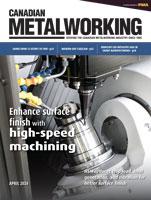
Keep up to date with the latest news, events, and technology for all things metal from our pair of monthly magazines written specifically for Canadian manufacturers!
Start Your Free Subscription- Trending Articles
Automating additive manufacturing
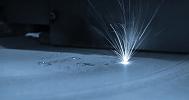
Sustainability Analyzer Tool helps users measure and reduce carbon footprint
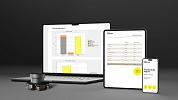
CTMA launches another round of Career-Ready program
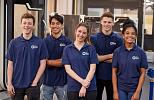
Sandvik Coromant hosts workforce development event empowering young women in manufacturing
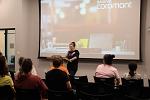
GF Machining Solutions names managing director and head of market region North and Central Americas
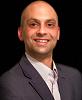
- Industry Events
MME Winnipeg
- April 30, 2024
- Winnipeg, ON Canada
CTMA Economic Uncertainty: Helping You Navigate Windsor Seminar
- April 30, 2024
- Windsor, ON Canada
CTMA Economic Uncertainty: Helping You Navigate Kitchener Seminar
- May 2, 2024
- Kitchener, ON Canada
Automate 2024
- May 6 - 9, 2024
- Chicago, IL
ANCA Open House
- May 7 - 8, 2024
- Wixom, MI