- FMA
- The Fabricator
- FABTECH
- Canadian Metalworking
Shield your lathe operators from risky operations
Protective machine accessories, proper operator PPE, and shop-wide training reduce hazards.
- By Sue Roberts
- April 10, 2018
- Article
- Metalworking
Editor’s Note: This article is based on the webinar “Safeguarding Basics Mini Webinar: Lathes & Grinder,”s presented by Rockford Systems LLC. The webinar is part of an ongoing educational series available to industry members at no cost. Visit www.rockfordsystems.com for information on upcoming safety presentations or to view past webinars.
Less than 50 per cent of industrial machines are properly safeguarded. The unfortunate result is thousands of reported amputations, lacerations, crushing injuries, and abrasions, and hundreds of accidents that result in deaths each year. The number of moving parts and motions involved in producing components on lathes and grinders and the proximity of operators during setup and operation can create particularly precarious situations.
Hazards to the operator and other employees in the machine area exist at the point of operation because of the very nature of the process; numerous rotating parts can create in-going nip points, pulling in clothing, hair, or fingers; chips and parts can fly off during production, endangering vision and creating a trip hazard around the machine; and coolant can spatter, causing slip hazards.
To provide a safe work environment, a company needs to keep current on—and follow—codes regarding proper machine guarding and personal protection equipment. All employees should be aware of the safety requirements for each machine and receive frequent reminders that safety procedures are expected to be followed at all times.
Danger and precaution signs strategically located on the machines can help keep dangers top-of-mind.
Shield Shop Employees
Shields secured to the lathe, probably the most common safety practice, can protect operators from several dangers, including the rotating chuck and tool, cross-slide movements, and the operation of the magnetic base.
A hinged chuck can prevent items from inadvertently getting entangled with the chuck. Some chuck shields are constructed entirely of steel; some have a steel frame with a visibility window to allow viewing during operation; and others are constructed of transparent, high-impact polycarbonate, providing a full view of the operation.
Chip/coolant shields can stop flying chips or parts from reaching the operator’s upper body or accumulating on the floor where they can create a slip hazard along with coolant overspray. Cross-slide travel shields travel along with the sliding carriage to provide continuous protection. Even if the operator is wearing proper personal protective equipment flying chips and coolant can create hazards, and the additional protection is recommended.
Most shields can be interlocked with the machine’s electrical system to prevent operation when they are not in place. Swinging a shield from its protective position will break its electrical connection and cut the power, forcing a quick coast down.
Lathe components like lead screws, cam shafts, and traverse rods that rotate slowly may appear to be harmless but they can hold a lot of torque, and their rotational energy can capture, pull-in, and crush items that get too close.
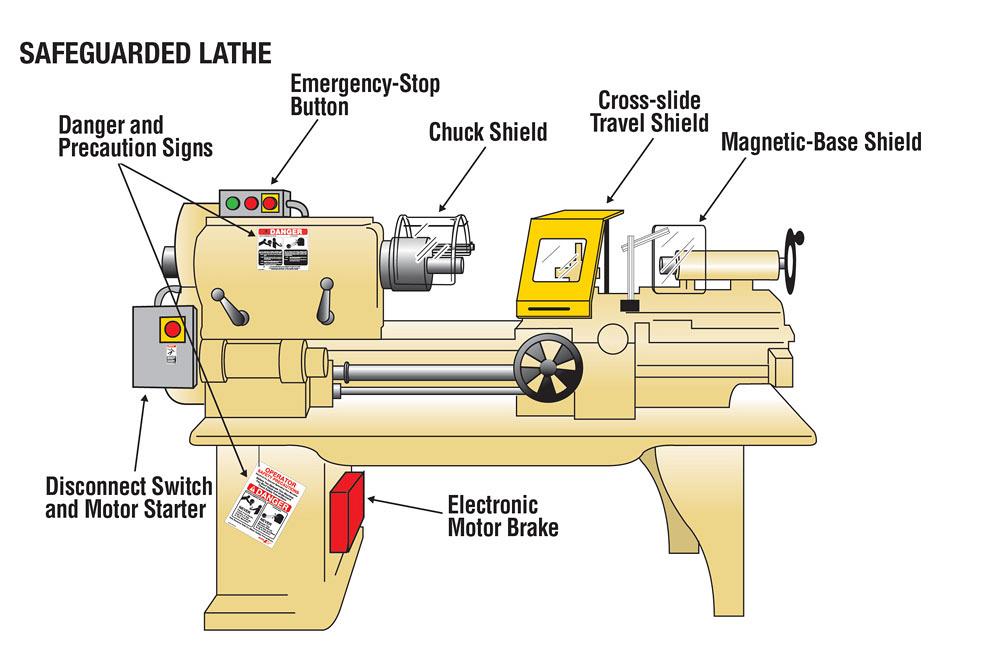
Proper guarding protects the operator and other employees from hazards such as those created at the point of operation and by ingoing nip points, rotating parts, flying chips and sparks, and spraying coolant.
Telescopic stainless steel sleeves can cover these types of rotating components allowing them to function while providing a safety barrier between the action and employees. A small amount of carriage travel will be lost and the sleeves will need to be cleaned and lubricated occasionally.
Boost the Power of ‘Stop’
Electrical updates for lathes can include the addition of emergency stop (e-stop) buttons that are main power disconnect switches to stop all machine activity.
American National Standards Institute (ANSI) standards say that an e-stop is required on any machine that will tolerate a quick stop. Some lathes have a true emergency stop built in to halt operation in less than a second, but most require several seconds to cease functions. An electronic motor brake can improve coast-down time, in some cases from 15 seconds to 3 seconds, which can make a significant difference in an emergency.
The red, mushroom-shaped button should have a manual latch that keeps it down once it is pushed to prevent machine operation by the regular controls. Once the e-stop is engaged, the latch keeps it down until a manual quarter-turn releases the latch and allows the machine’s controls to again command the machine’s actions. Kick plates or grab-wires that go across a machine can facilitate an emergency shut-down if there is potential for an operator’s hands to be caught.
E-stops need to be readily accessible. An e-stop button should be within easy reach at each location on the machine that requires operator interaction. When more than one individual is involved, each person should have his or her own e-stop.
A spring-loaded button indicates that there is a magnetic motor start or anti-restart, also known as drop-out protection, to prevent a machine from unexpectedly resuming operation after shutting down because of power loss.
Avoid Flying Wrench Risks
Misuse of a standard chuck wrench is a common source of lathe accidents.When a lathe is not in use, a seemingly logical and typical but unsafe storage place for the chuck wrench is in the chuck. The danger is that an operator may turn on the lathe without checking to see where the wrench is located. It can fly out of the chuck, and across the shop, causing a serious injury to anyone in the area.
Spring-loaded, self-ejecting chuck wrenches, available in several sizes, can eliminate this hazard by not allowing the wrench to remain in the chuck. They are available in several sizes.
Onsite risk assessments and machine surveys can help a company get and stay up to code. Based on ANSI B11.0-2015, a risk assessment provides a hazard score with the risk level for each machine, suggestions to lower the hazard level, and detailed documentation to outline the results. A machine safeguarding assessment audits each machine for code compliance and provides customized proposals that suggest specific products and services to bring the machine into compliance.
Safety principles when working with a lathe, according to the Canadian Centre for Occupational Health and safety (CCOHS), include:- Wear appropriate safety glasses during operation.
- Remove entanglement hazards such as loose clothing and jewelry.
- Keep the floor should be clear of obstructions and slip hazards.
- Ensure the e-stop button is within easy reach of the operator.
- Follow job specifications for speed, feed, and depth of cut for the material being turned and take all necessary steps to ensure that work is run true and centered.
- Centre drill work deeply enough to provide support for the piece while it is turning.
- Secure and clamp the workpiece.
- Adjust the tool and tool rest so they are slightly above the centre of the work.
- Use a lifting device to handle heavy chucks or work.
- Inspect chucks for wear or damage to help prevent flying workpieces.
- Use a barrier guard when operating a lathe in a semi-automatic or automatic mode.
- Guard all power transmission parts.
- Remove all tools, measuring instruments, and other objects from the saddle or lathe bed before starting the machine.
- Keep all cutting tools sharp.
- Ensure that the clip and coolant shields are in place.
- Shut off the power supply to the motor before mounting or removing accessories.
- Stop the lathe before taking measurements of any kind.
- Use a vacuum, brush, or rake to remove cuttings only after the lathe has stopped moving.
- Keep working surfaces clean of scrap, tools, and materials.
- Keep the floor around the lathe clean and free of oil and grease.
Visit www.ccohs.ca for safety information when working with any metalworking equipment.
Rockford Systems LLC, www.rockfordsystems.com
About the Author
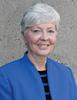
Sue Roberts
2135 Point Blvd
Elgin, IL 60123
815-227-8241
Sue Roberts, associate editor, contributes to both Canadian Metalworking and Canadian Fabricating & Welding. A metalworking industry veteran, she has contributed to marketing communications efforts and written B2B articles for the metal forming and fabricating, agriculture, food, financial, and regional tourism industries.
Roberts is a Northern Illinois University journalism graduate.
subscribe now
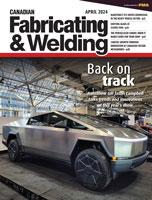
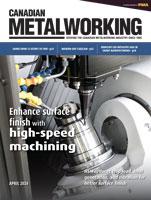
Keep up to date with the latest news, events, and technology for all things metal from our pair of monthly magazines written specifically for Canadian manufacturers!
Start Your Free Subscription- Trending Articles
Automating additive manufacturing
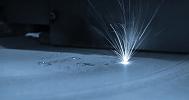
Sustainability Analyzer Tool helps users measure and reduce carbon footprint
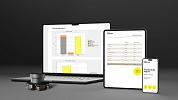
CTMA launches another round of Career-Ready program
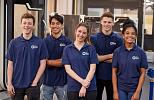
Sandvik Coromant hosts workforce development event empowering young women in manufacturing
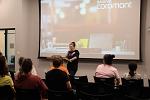
GF Machining Solutions names managing director and head of market region North and Central Americas
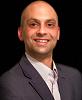
- Industry Events
MME Winnipeg
- April 30, 2024
- Winnipeg, ON Canada
CTMA Economic Uncertainty: Helping You Navigate Windsor Seminar
- April 30, 2024
- Windsor, ON Canada
CTMA Economic Uncertainty: Helping You Navigate Kitchener Seminar
- May 2, 2024
- Kitchener, ON Canada
Automate 2024
- May 6 - 9, 2024
- Chicago, IL
ANCA Open House
- May 7 - 8, 2024
- Wixom, MI