- FMA
- The Fabricator
- FABTECH
- Canadian Metalworking
Ingenuity handles oversized projects
HL Enterprises barges ahead on the Sunshine Coast
- By Sue Roberts
- March 7, 2018
- Article
- Made In Canada
The HiBaller V wasn’t the first barge built by the certified welders and fabricators at HL Enterprises Inc. in Gibsons, B.C., but it is certainly the largest. Most likely it’s the largest steel barge manufactured in a fabricating shop along B.C.’s Sunshine Coast.
Contracted by HiBaller Marine Transportation, a company that loads out of Sechelt, B.C., to haul vehicles, building materials, and supplies, the new craft measures 100 ft. long by 36 ft. wide by 6 ft. high and has a maximum capacity of 300 tons. It made quite a splash when its 150 tons slid into the water in Port Mellon, about 22 miles north of its construction location.
Fully understanding that the roads and highways between HL Enterprises and the launch site wouldn’t accommodate moving the completed barge, Richard Beauvais, owner of HL Enterprises along, with his wife Sonja explained that they had to design the HiBaller V so it could be split into two 18-ft.-wide by 100-ft.-long sections that could be trucked down the highway. The sections were welded together shoreside before the barge was set afloat in Howe Sound.
During construction, the two sections were tacked together so they could be easily separated, but the barge was still considered one piece during the build. All-Tow Boat Moving Ltd. in Delta, B.C., moved the two mirror sections of the barge on consecutive nights and positioned them on I-beams in preparation for final welding.
Tayte Nelson, shop foreman, said, “We built in a seam that we weren’t going to finish out and weld during construction. When it came time to move the barge, we used a hydraulic jack to separate the two parts. When we got to the launch site, our boat mover got the sections quite close together. Then we used the same jacks to do the final lineup and push them back together for welding. The main challenge was the rain. We didn’t have much cover so we had to work quickly during a patchy clearing in the weather.”
Tolerances, important to every job that comes into the shop, needed extra attention when building the HiBaller V to ensure final fit-up. “For building a barge that long, everything had to be pretty bang on. We couldn’t have wavy deck plates or anything like that. We used a laser level and worked within 0.125-in. standards,” said Nelson.
Choosing Local
HiBaller and HL Enterprises had a long-standing and comfortable working relationship before embarking on the HiBaller V project. HL had built smaller barges, a landing craft, and accessories for aluminum boats for the transportation company. Still, when John Smith, owner of HiBaller Marine, decided he wanted the super-sized barge, he considered working with an overseas builder.
“I was originally going to have the barge built in China, but they are not even close to the standard of workmanship that we have here locally. The barges built by HL are quite a bit more substantial in terms of framing and basic construction than those from many other builders. Going with HL gave me the good quality, a good price, and it helped keep local guys working,” Smith said.
“Both the marine surveyor who checked the barge for federal registration and the representative from my insurance company went through the barge and didn’t have one issue. They were both impressed with the workmanship.
“I’ve had quite a few barges built, and I’ve built three of them myself, so I knew exactly what I wanted size-wise. We started with an enlarged set of drawings that I already had. Nelson at HL put the finishing touches on the plans. Then we built it,” said Smith. “My family has lived in Gibsons for 98 years, and the whole town was interested in seeing what we were doing with this project.”
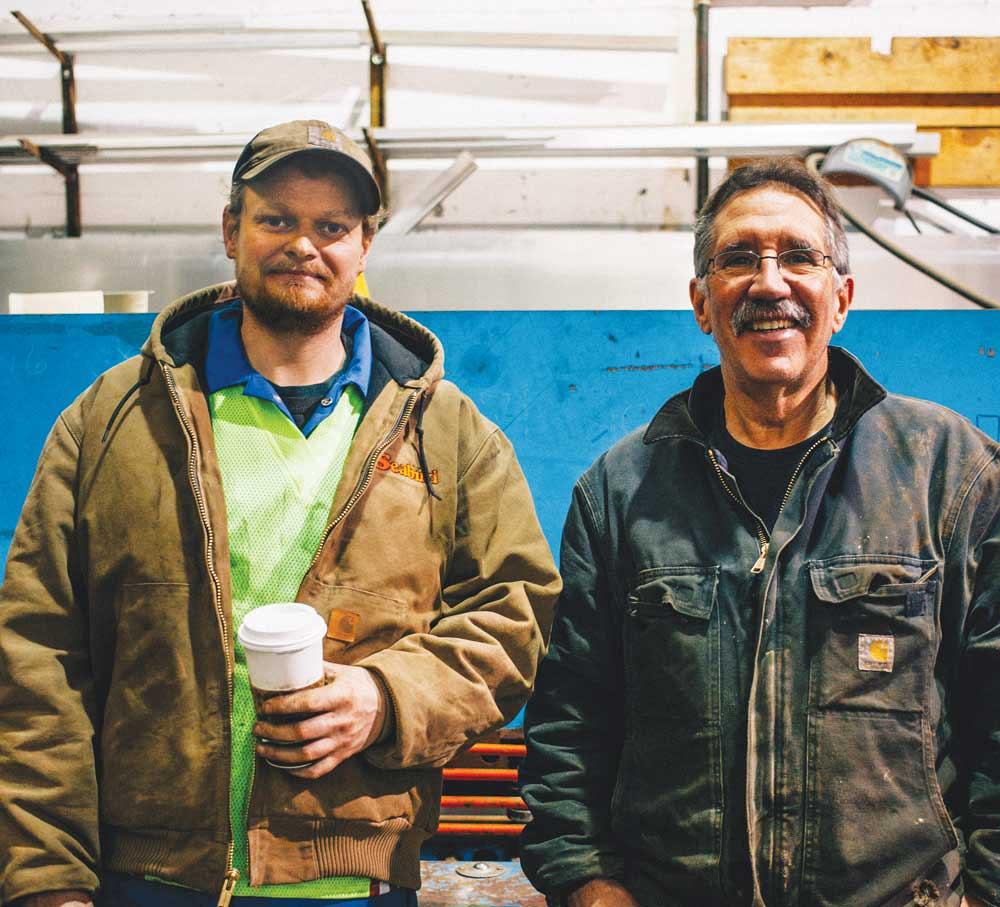
HL Enterprises Shop Foreman Tayte Nelson and owner Richard Beauvais pause in front of the shop’s Union shear.
Building Outside the Box
The size of the barge made it necessary to handle the project outside of the 60- by 120-ft. shop. HL Enterprises poured a cement slab next to the building to support its construction. Before HiBaller V was completed, the slab and frame were covered by a 40- by 80-ft. Quonset-style tent to protect the work and the workers from the elements.
Components were fabricated in the shop using a 10-ft. hydraulic shear, 10-ft. press brake, a cutting table, and 150-ton ironworker. Eight Lincoln suitcase welding machines, a half-dozen 300-amp units and four mobile diesel-powered welding machines were available to put the barge together.
The hut now houses work on a smaller barge that won’t pose transportation problems once completed. It is one of four barges ordered since the HiBaller V launched. “We are building a barge for Harlow Marine International in Langley, B.C., right now, and we have another one scheduled for the summer,” said Nelson. Harlow is a marine broker and consultant firm that works like a real estate agent for used and new commercial craft.
Although HL Enterprises seems to be a small company specializing in barges, its team of about a dozen people total is known for doing any type of custom metal fabrication and machining needed. A milling machine and several lathes, including a 14-ft. Microcut lathe, comprise the company’s machine shop. Most projects involve fabricating and welding, many require both fabricating and machining capabilities, and 15 to 18 per cent are completed in the machine shop.
It’s fine if a job comes along with its own design and fine if it doesn’t. The company will work with a customer to develop drawings from the idea stage or fine-tune existing drawings to achieve the best, most economical outcome. In an average month, they work through about 100,000 lbs. of material, including aluminum angle iron; bar stock; welded screens and grates; and mild, hard, and stainless sheet and plate.
Teapots to Tugboats
“We’re open to the public to take care of whatever needs building or repair,” said Nelson. “There could be 10 to 20 customers a day wanting anything from short pieces of material to be cut to welding a fry pan back together to building a frame of some sort.” As the company website points out, they take care of everything from “teapots to tugboats.”
Between five and 15 projects, depending on their size, will be in progress at any one time. In an average year, completed projects of a variety of sizes can easily top 500. Residential and commercial construction jobs include beams and foundations, staircases, canopies, and countertops. Seismic upgrades and renovations on commercial, residential, and educational buildings are also part of the services. The company builds a variety of sizes of Transport Canada-certified boats with side, center, or back consoles.
And there is the artistic side to HL Enterprises. Its expertise in working with structural elements contributed to building the 16-ft.-tall “Dancing Tower” sculpture that graces the outside entrance to the Arts Council of Surrey, B.C. Fabricated aluminum pipes support tempered coloured glass panels that create moving, dancing patterns as the sun passes overhead.
Expanding Horizons
The business is expanding its reach across the country, working with customers in Saskatchewan and Manitoba, and is adding international companies to its client roster. It is currently working on a landing craft order for a company in Belize. “Canadian standards for shipping and vessel construction are so high that if we build to our standards, we are exceeding the requirements in other countries,” said Nelson.
A second location, prompted by the HiBaller V project, is in the works. “We are looking at buying about half of 9 acres on the waterfront in Port Mellon to expand our barge and tugboat building. It will house our marine jobs,” said Beauvais. “The new facility will have about the same equipment as our current shop. We’ve already purchased some items that are waiting for the new location, and we plan on purchasing some more large equipment to help us manage the large projects.”
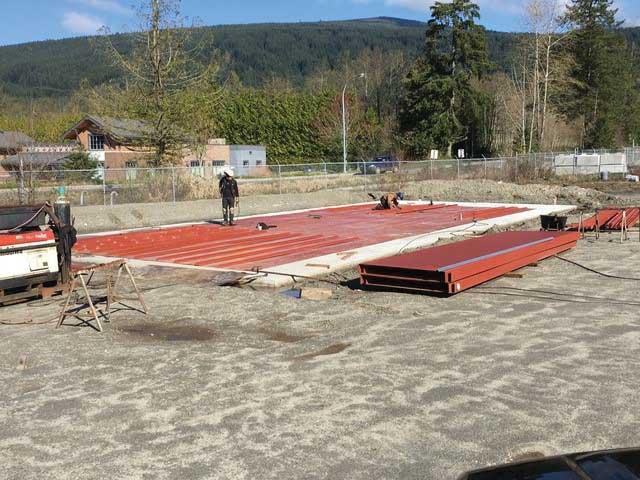
The size of the HiBaller V forced construction to begin on a cement slab outside of the HL Enterprises shop. Photo courtesy of HiBaller Marine Transportation.
Beauvais leads a double life. He serves as the point man for a quickly growing metal fabrication and metalworking business, which could be plenty to keep a business owner busy, but he may or may not be available at the shop. He might be working on one of his own commercial fishing boats. It was his fishing operation that prompted his purchase of the shop.
“I bought HL Enterprises in 2007 to do mostly my own marine work. At that time a partner and I had seven fishing boats,” Beauvais said. By owning the shop, Beauvais avoids waiting for service when one of his vessels needs maintenance or repairs. His own marine jobs manage to work right into the production schedule.
Photos courtesy by Nik Muryn, Make Waves Media House, unless otherwise noted.
All-Tow Boat Moving Ltd., www.alltowboatmoving.ca
HiBaller Marine Transportation, www.hiballertransportation.com
HL Enterprises Inc., www.hlenterprises.ca
About the Author
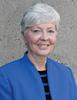
Sue Roberts
2135 Point Blvd
Elgin, IL 60123
815-227-8241
Sue Roberts, associate editor, contributes to both Canadian Metalworking and Canadian Fabricating & Welding. A metalworking industry veteran, she has contributed to marketing communications efforts and written B2B articles for the metal forming and fabricating, agriculture, food, financial, and regional tourism industries.
Roberts is a Northern Illinois University journalism graduate.
subscribe now
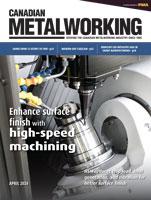
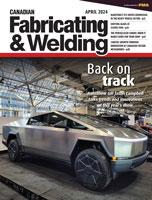
Keep up to date with the latest news, events, and technology for all things metal from our pair of monthly magazines written specifically for Canadian manufacturers!
Start Your Free Subscription- Trending Articles
Aluminum MIG welding wire upgraded with a proprietary and patented surface treatment technology
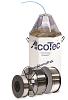
Achieving success with mechanized plasma cutting
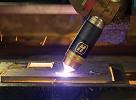
Hypertherm Associates partners with Rapyuta Robotics
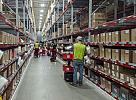
Gema welcomes controller

Brushless copper tubing cutter adjusts to ODs up to 2-1/8 in.
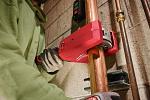
- Industry Events
MME Winnipeg
- April 30, 2024
- Winnipeg, ON Canada
CTMA Economic Uncertainty: Helping You Navigate Windsor Seminar
- April 30, 2024
- Windsor, ON Canada
CTMA Economic Uncertainty: Helping You Navigate Kitchener Seminar
- May 2, 2024
- Kitchener, ON Canada
Automate 2024
- May 6 - 9, 2024
- Chicago, IL
ANCA Open House
- May 7 - 8, 2024
- Wixom, MI