- FMA
- The Fabricator
- FABTECH
- Canadian Metalworking
Technology Spotlight: Tube and pipe storage measures up
Save space, improve safety, and increase production with vertical material storage systems
- By Sue Roberts
- April 9, 2018
- Article
- Fabricating
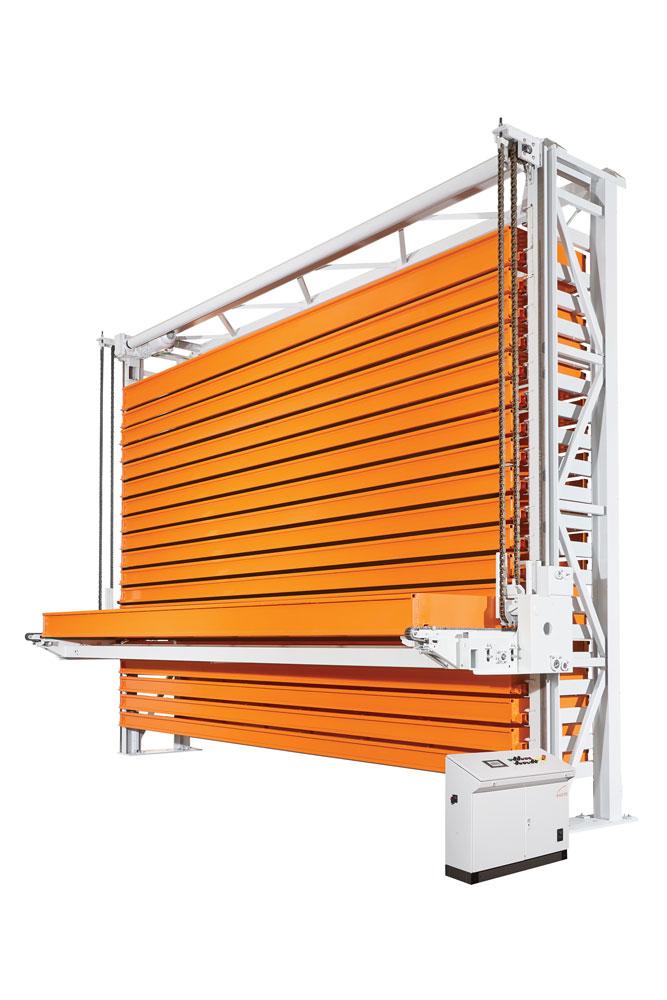
KASTOecostore systems use typically wasted vertical space to store materials including tubes, pipes, bars, and sheet in cassettes that can safely deliver the materials for processing.
Components formed from tubes and pipes are indispensable in nearly every industry. From large steel pipes used in construction to the myriad sizes, shapes, and materials that comprise tubes involved in vehicle production to aluminum tubes prevalent in furniture manufacturing, these hollow, often circular hard-to-handle products need to be stored and safely moved to the saw or fabricating process.
Storage of these long, awkward, often heavy products can require an inordinate amount of floor space. Moving them can be time-intensive and present safety hazards … issues that fabricating shop owners work to avoid.
Canadian Fabricating & Welding talked with Kasto Inc.’s Nikolis Wasynczuk, vice president, and Hermann Schulte auf’m Erley, storage retrieval systems sales manager, about how small and mid-sized facilities can use a tower system to safely and economically store tube and pipe and how a small tower system can fit into--and improve--production flow.
A Flexible System
“Our KASTOecostore is a simple, automatic system that can be configured for tube and pipe storage,” said Schulte auf’m Erley. “It’s smaller and at a lower cost than the more elaborate systems for steel distribution centers and large production houses. It works well when it feeds one or two saws or fabricating processes.”
A KASTOecostore fits in a footprint of about 25 by 8 ft. Although compact, the large-format storage area of the standard system accommodates tube and pipe up to about 21 ft. long in cassettes that are 33 inches deep.
The cassettes surround and secure the materials, preventing them from rolling or dropping, and protect the ends from damage during automated transport. The amount of vertical space between the cassettes can be based on the diameters and weights of the materials to be stored. Height between the cassettes can be up to 17 in., and various configurations are possible.
Cassettes, available in three different loading heights, can be chosen to accommodate either 1.2 or 3 metric tons each.
Production requirements and space availability determine the number of cassettes to be stacked within the system’s frame up to about 26 ft.
Schulte auf’m Erley said, “If you have very low ceilings, we can work with that, but the higher you can go, the lower the storage costs. We’ve built some of our larger UNITOWER systems outside, in pits, or through the roof to increase the storage capacity.”
Storage-enhanced Productivity
Wasynczuk said, “It is easy to add on to a building for material storage, but it gets to a point where either there isn’t more space or material handling inefficiencies start to increase and add on to the cost of producing a part.
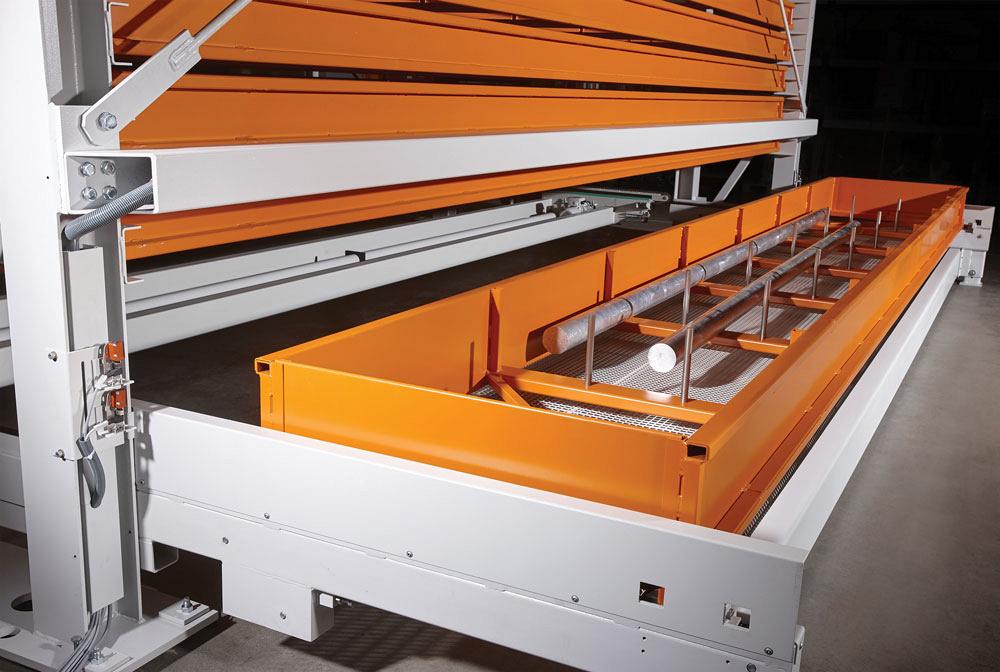
Pegs can be used to divide each cassette into subcompartments to store different types of or sizes of tubes, pipes, and bar materials.
“Storing bulky, hard-to-handle materials in a condensed, vertical space makes sense. Fabricators are starting to open their eyes to the efficiencies of using the third dimension of their shops for this, and that is making it easier to justify the expenditure.”
Once the decision is made to add a vertical storage system, its addition is typically incorporated into a remodelling effort to tweak, or completely re-create, the shop layout to allow the material to quickly flow from the tower to processing equipment for increased productivity, said Schulte auf’m Erley. Rather than requiring a forklift driver and one or two other employees to move material, the cassette of material is shuttled to the job. The people previously involved with material handling can be reassigned to other positions.
“Timewise it takes about two minutes to get a new cassette of tube or pipe, not a half hour of time from multiple employees,” he said. “A tower system is a one-man operation typically handled by the operator of the saw or fabricating equipment who can be taking care of two or three processes.”
The company’s SmartControl software pairs with an intuitive touchscreen to control the system. Although the basic storage tower system doesn’t have designated inventory control, Wasynczuk said that there are several ways the more advanced controls on the larger UNITOWER systems can be linked with a shop’s existing software to track material location and inventories.
Schulte auf’m Erley said, “With the smaller systems, many people label the cassettes for easy identification so the operator knows where the material is. He just types in the number of the cassette and the system brings it down. It is loaded or unloaded as needed and returned to its location.”Insert pegs can be used to create subcompartments within each cassette to allow it to store more than one type or size of material.
Add in Safety
Using a tower system can be a plus on the safety side.
Wasynczuk said, “The weight of a long piece of tube or pipe can be unevenly distributed when it is lifted by a forklift. There’s a danger that the forks won’t be centred under the load. With lifting an uneven load, a tube or pipe can roll off, or pieces can shift during transport and tip the entire load off the forks, creating safety hazards for the people moving the material and others in the area. And the ends of the material can be damaged or the surface scratched, causing scrap. When the material is stored in a tower’s cassette and automatically moved, these hazards are eliminated.
“Small shops are adding vertical storage for three reasons. They want to be more efficient, they want to save floor space, and they want to be safer.”
Kasto Inc., www.kasto.com
About the Author
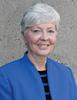
Sue Roberts
2135 Point Blvd
Elgin, IL 60123
815-227-8241
Sue Roberts, associate editor, contributes to both Canadian Metalworking and Canadian Fabricating & Welding. A metalworking industry veteran, she has contributed to marketing communications efforts and written B2B articles for the metal forming and fabricating, agriculture, food, financial, and regional tourism industries.
Roberts is a Northern Illinois University journalism graduate.
subscribe now
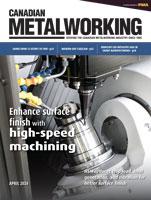
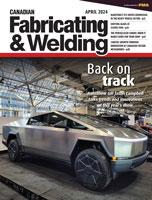
Keep up to date with the latest news, events, and technology for all things metal from our pair of monthly magazines written specifically for Canadian manufacturers!
Start Your Free Subscription- Trending Articles
Aluminum MIG welding wire upgraded with a proprietary and patented surface treatment technology
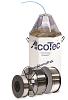
Achieving success with mechanized plasma cutting
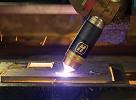
Hypertherm Associates partners with Rapyuta Robotics
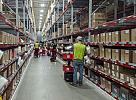
Gema welcomes controller

Brushless copper tubing cutter adjusts to ODs up to 2-1/8 in.
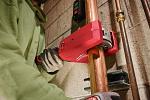
- Industry Events
MME Winnipeg
- April 30, 2024
- Winnipeg, ON Canada
CTMA Economic Uncertainty: Helping You Navigate Windsor Seminar
- April 30, 2024
- Windsor, ON Canada
CTMA Economic Uncertainty: Helping You Navigate Kitchener Seminar
- May 2, 2024
- Kitchener, ON Canada
Automate 2024
- May 6 - 9, 2024
- Chicago, IL
ANCA Open House
- May 7 - 8, 2024
- Wixom, MI